Remanufactured Gen VI Vortec 7.4L, 454 Marine Longblock. Replaces years 1996-newer.
Marine Engines 4 Less
Write a Review

Marine Engines 4 Less
Remanufactured Gen VI Vortec 7.4L, 454 Marine Longblock. Replaces years 1996-newer.
Description
Remanufactured Gen VI Vortec 7.4L, 454 CID Marine Longblock. Replaces years 1996-newer.
Completely remanufactured 7.4L, 454 CID Gen VI marine engine longblock. The longblock comes assembled with all internal components, cylinder heads, and gasket kit and oil pump. The only components that are remanufactured in this assembly is the engine block, cylinder heads, crankshaft, and connecting rods. All remaining components are new.
- Gen VI 1996-newer
- Block casting numbers: 297
- Head casting number: 279
- 1-PC Rear Main Seal
- Hydraulic Roller Camshaft
- Oval Intake Ports
- Uses 6 bolt Aluminum Timing Cover
This is a perfect stock replacement for those engines that have suffered from a cracked block due to improper winterization or another type of engine failure.
Specifications:
- 1 Piece Rear Main Seal
- Standard rotation
- Cylinders: 90 Degree V8 Cylinder
- Hydralic Roller Camshaft
- Composition Ratio: 8.75:1
- Bore: Standard
- Firing Order: 1-8-4-3-6-5-7-2
- Oil Pan Capacity: 8 quarts
- Oil Type: SAE 15W40 Pennzoil Marine
- Horsepower: 340 hp @ 4400 RPM (4bbl carbureted)
- Torque: 435 lb-ft @ 3200 RPM
Learn more about or remanufacturing process below.
Our Remanufactured Engines
With our 40 years in the engine business we have learned over years what parts and processes work the most effectively to produce a quality unit. With that information we have a Premiere Multi-Step Method that we use to remanufacture our engines.
Only the Best Blocks:
- We start by selecting only the "healthiest" blocks. No cracks, no rust, no signs of abuse, no signs of salt water use.
- We completely disassemble the blocks and vigorously clean them along with the cylinder heads and crankshafts. We use a thermal cleaning process which includes baking them in an oven to remove core material and running them through a stainless steel shot machine to clean them to machinable metal.
- We then demagnetize the engine blocks before machining them on our CNC machine to insure precise OE specifications.
Figure 1: Here, a line of remanufactured 4.3L engines are being built on one of our three assembly conveyors.
We measure cylinder bores three times:
- As an example of our passion for perfection, after we bore, hone and plateau brush all cylinder walls, we measure them three times to ten-thousandths of an inch.
- Bore sizes will rarely be over .030.
- We know this extra dedication will pay off for you in performance and dependability.
Figure 2: All of our engine blocks are bored, decked, and blueprinted on CNC equipment. Here, you can see a 5.0L engine block being "probed" so that the bore will be to exact OEM specifications.
Figure 3: Here, you can see a 5.0L block being honed to exact sizing. We use diamond tooling to create pristine cross-hatches for prefect piston ring clearance and function.
New internal parts, marine gaskets:
- We install vital new internal parts, including new hypereutectic (heatfighting) pistons where available, new premium piston ring sets, new engine bearings, new valves, new camshafts, new springs, new lifters, new timing components and new tinware (where applicable).
We also install special marine head gaskets-steel, copper or copper clad, whatever the application demands:
- We always use brass or stainless steel expansion plugs. ALL parts we install meet or exceed original manufacturers' specs. Many parts are actually better than original equipment. We pick up running changes to eliminate problems common in the original engine.
The Final Touch:
- After our expert technicians have completed all critical machining operations and the components have been washed, our assembly team takes over.
- We pre-lubricate camshafts and pistons.
- Once assembled, we spin test every assembled engine on our Sim-Test machine while our technician logs the compression and oil pressure for future reference.
- After a complete final inspection before shipping…your Marine Engines 4 Less remanufactured engine is fully functional and ready to go.
Figure 4: All of our engines, new and remanufactured get SIM tested before shipping. This process involves checking each cylinder to appropriate compression readings, priming the top end valve train and oil pump, inspecting for oil leaks and noises. The helps to insure that the end user gets a quality product free from imperfections and quality issues.
OUR SHIPPING POLICY
Domestic:
We strive to ship our products as quickly as possible. Most in stock small package (part) items will ship the same business day as long as the purchase is made before 3PM EST. Some items will not ship the same day. For in stock engines, the shipping lead time is 1-3 business days depending on the part number. For engines that are not in stock there will be a lead time. The engine will not be available for purchase if it is an engine we cannot get or build. For up to date lead time information and for time sensitive orders, please reach out to Marine Engines 4 Less before you place the order. Please reach out via phone +1 888-364-4537, text +1 352-825-0335, or email info@marineengines4less.com to verify stock and availability for time sensitive shipments.
For small package (parts) shipments: we will ship by whichever method you select during checkout. Free shipping options (if applicable) will be shipped via UPS or FedEx ground. Free shipping is only available to customers within the continental USA. Shipments to Alaska, Hawaii, Puerto Rico, Guam, and other US territories are not eligible for free freight. International shipping options are available for our worldwide customers. We use UPS and FedEx to ship worldwide. VAT and any other customs charges are not covered by Marine Engines 4 Less. The carrier will reach out to you to collect those charges independently. Lead times on small part items are expressed in the ad. For time sensitive shipments, it is best to reach out to us to confirm availability before purchasing.
For freight item (engine) shipments: For larger and heavier shipments, LTL freight is used to ship. Shipping costs will be calculated in the shopping cart. It is imperative to put correct contact information down in the shipping details. Freight companies will often need to reach out to you to arrange an appointment, or to verify other details. Incorrect shipping details will only delay your delivery. For shipping rates outside the United States, please reach out to our sales team for shipping costs and options. The website cannot accurately calculate LTL freight shipment outside the United States. For international shipments, the freight costs do not include VAT and other duties/taxes that your respective country charges. For VAT, tax and duty estimates, please reach out to us.
Some LTL freight companies will charge more for deliveries deemed to be "limited access", residential, or require an appointment or lift gate. If you feel as though your shipment may need one of these accessoral options, please reach out to us for an accurate shipping quote.
International:
For Parts/Small Package Shipments:
For small engine parts less than 150 LBS, we ship via UPS or FedEx. Shipping rates will be calculated in your shopping cart. These shipping rates do not include VAT, duties, or customs charges that your respective country may charge.
For Engine Orders:
Our engines ship all over the world. We offer both ocean freight and air freight at competitive prices. To request a shipping quote please email us at info@marineengines4less.com with the following information:
- item part #
- desination country and postal code
Note: freight costs do not include VAT, duties, and other customs fees charged by the desination country. For an estimate on these costs, please request a quote before you buy.
We'll get back to you quickly with a shipping quote!
-
Worldwide Shipping
-
Hassle Free Returns
-
Reliable Customer Support
-
Easy Online Ordering
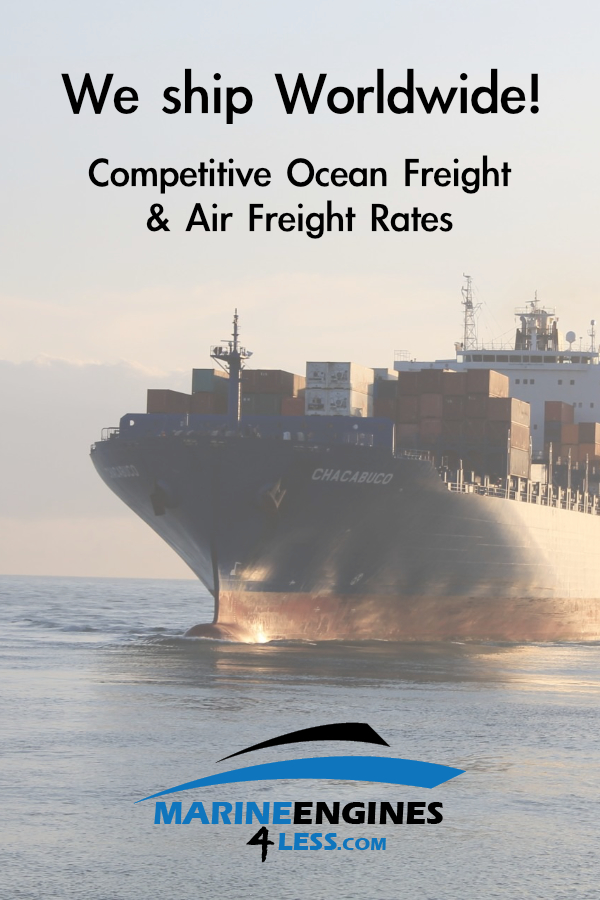